News and events:
The most recent manufacturer alignment offers Asphalt Shingle, Bitumen Built Up (Flat), and Single Ply roofing coupled with Metal, and Tile roof materials.
We are offering a wider range of Impact windows and doors.
Our window and door manufacturing options include local manufacturers well versed in the affects of wind during the hurricane season.
Window and door options include Wood, Fiberglass, Aluminum and Vinyl.
We are a member of the HomeAdvisor team.
|
- Welcome
- Roofs
- Hurricane Help
- Windows
- Doors
-
Projects
-
About
Us
-
Contact
Us
-
Glass
Types
-
Our President
21st Century Construction, Inc. is well versed in all types of roofing and we can help you plan your roof replacement today.
We assist each owner weighing the pro's and con's for the roof type desired, whether we are removing and replacing the roof with like for like materials or changing materials completely like moving from a shingle roof to a more wind resistant metal roof.
21st Century offers the product to suit the owners wants, needs, and desires in an aesthetically pleasing roofing system.
Asphalt shingle roofing
Asphalt shingle roofing has a long expected lifetime. Depending on the specific shingles you choose, you can expect your roof to last anywhere from 10 to 25+ years.
Bitumen roofing
Modified bitumen membranes are able to expand and contract with the rest of the roofing layers, and because they adhere directly to the substrate they do not need to be covered with gravel, although they do need a UV-protective coating (granules).
Torchdown or peel-and-stick is a sensible choice when flammability of the substrate or surrounding materials is a concern.
Single Ply roofing
Single Ply roofing have far fewer seams than asphaltic rolled roof systems and don't require dangerous torches or hot asphalt for installation. They also come with prefabricated detailing accessories that make installation easy.
Metal roofing
While other roofs quickly diminish in value as they age, metal roofs provide the following lasting benefits:
1. Proven performance expectation of 50+ years.
2. Beautiful styles to match any home or neighborhood.
3. Interlocking panels for maximum wind resistance.
4. Fire resistance.
5. Energy efficiency by keeping homes cooler.
Tile Roof
Tile roofing can last more than 100 years when in the right climate. Clay and concrete tile roofs have been known to withstand heavy rains, hail, high winds, and even fire.
We recently became full time residents of Perry, we moved to Perry because we fell in love with the lifestyle in Perry and in Taylor County. Our attraction was realized while helping family and friends after Hurricane Idalia.
We moved to Perry as full-time residents to relax and maybe even retire, then came the weather forecast with three hurricanes in 13 months, Hurricane Idalia in August 2023, Hurricane Debby in August 2024, and Hurricane Helene in September 2024. Our passion before moving to Perry was construction, which we put behind us because we were on the road to retirement. After experiencing the past 13 months, we are slipping back into construction to help the fine people affected by the hurricanes in Taylor and surrounding counties.
21st Century Construction is a Florida Certified General Contracting and Certified Roofing firm. Given the chance to assist, we are offering help in this time of need.
Our services include, but are not limited to:
- Complete rebuilds of commercial, residential, and agricultural structures
- Roof replacement and roof repair on commercial, residential, and agricultural structures
- Exterior repair on commercial, residential, and agricultural structures
- Interior repair to commercial, residential, and agricultural structures
Able to begin helping today, we offer no cost property inspections, no cost estimates, reasonable and fair pricing schedule.
Please check the validity of the credentials of each company hired to help you. DO NOT BECOME A VICTIM in your time of need. No matter who you plan to hire, checking the credentials should be easy to do right on your phone.
Our license numbers are listed below.
CGC1527754 State Certified General Contractor
CCC1334908 State Certified Roofing Contractor
Link to DBPR for license verification. This link will work for anyones license.
Link to DBPR Disaster Contractor Search This link is company specific.
Please feel free to contact us for any assistance needed.
Timothy (Tim) Cooprider
561-756-2145
YES! WE CAN HELP YOU
WITH WINDOWS!
Have you looked into new windows recently?
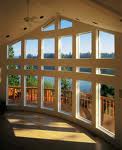 |
Will the new window be impact resistant?
Does it have a shutter system installed?
Would you like a window with a grid or clear view?
Do you know what color you would like to have?
Have you considered material type, Aluminum, Vinyl, or Wood?
Is the window you are replacing a single window opening, or is there a mullion bar between two windows?
Does the window have a seat you can set on inside, or are three windows together like a bay window?
Do you know what Low E means?
Does the new window need to be insulated glass?
Will the glass be clear or tinted?
If this is your first window experience, many questions need to be answered before you jump into your installation process. Once you have decided what color, size, shape, and material you want, now it is time to find a manufacturer that can supply all of the variables in a single window package. Which manufacturer is the best? What windows will last the longest? Who did the most testing on the product I am buying? All questions you will want answered. |
|
|
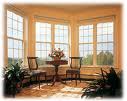 |
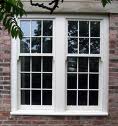 |
|
This is where 21st Century Construction, Inc. can give you some assistance.
We work with more than one window manufacturers product and feel like we can
furnish the window that will best meet your needs!
YES, WE CAN HELP YOU
WITH DOORS!
But first you need to make a few decisions.
Do you know the right questions to ask in order
to get the door that best suits your needs? |
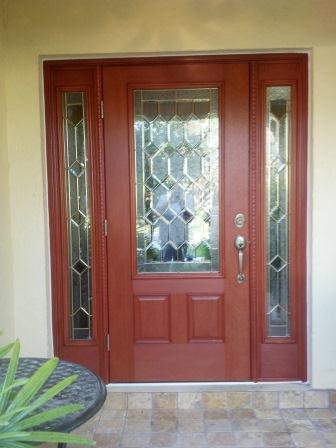 |
Do you need an interior or exterior door?
Do you need a fire rated assembly like the door between the garage and the house?
Does the door you are putting in have shutters installed, or will you need impact resistant?
Are you looking for a door with a glass installed?
Have you considered the style and look you want for the hardware and lockset?
What about the trim, did you have a special trim in mind; are you wanting a new look inside?
Have you considered the texture and color of your new door?
Do you want it to look like wood or are you considering a more modern appearance?
Do you know what you want the door made of; a composite material, Aluminum, Steel, or Wood? |
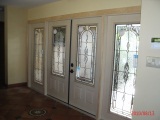 |
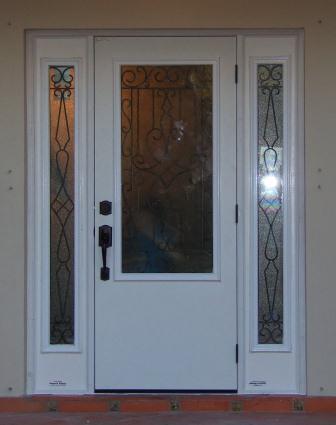 |
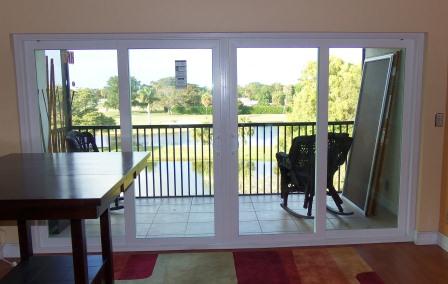 |
- Intro
- Shingle
Roofs
- Metal / BU
Projects
- Lake Mary
Bridge
- Caicos Airport
Terminal
- Tilt Wall
- Remodels
- Windows
& Doors
As you look through some of the past projects we assembled here,
please keep in mind these are all past projects used to help the viewer better understand the capabilities of the remarkable installers in our organization.
With the remodeling world taking all the twists and turns in
today's environment we strive to keep abreast of the technological advances in the market today. Some of the recent remodels have included WIFI controled equipment to assist with lighting and temperature control.
Along with interior remodels, our installation crews are well versed in the installation process for windows and doors. The windows and doors can be installed in new construction or retrofit applications.
Please enjoy your visit and thank you for visiting the 21st Century Construction, Inc. website.
21st Century Construction, Inc.
Some of the shingle roofs
depicted below are close to the end of their useful life. Although a roof is seldom at the top of our list for maintenance, repair, or replacement, if the roof on your home looks like the last three roofs pictured here you may want to consider
completing the roof replacement prior to experiencing the high winds associated with a major storm.
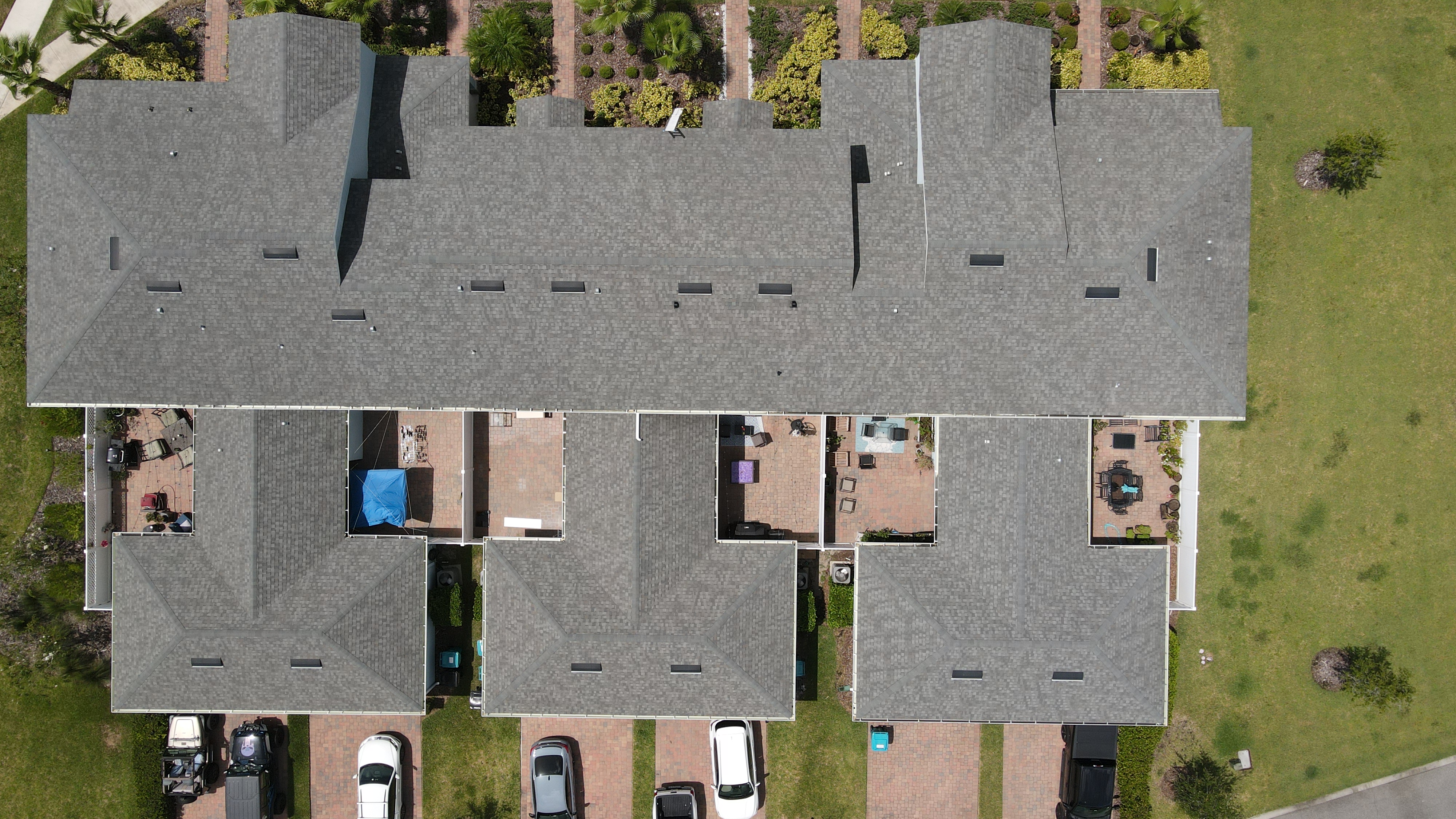 |
The photo shows an aerial view of a shingle roof recently completed.
This is a 6 unit town home with attached garage and walkway. |
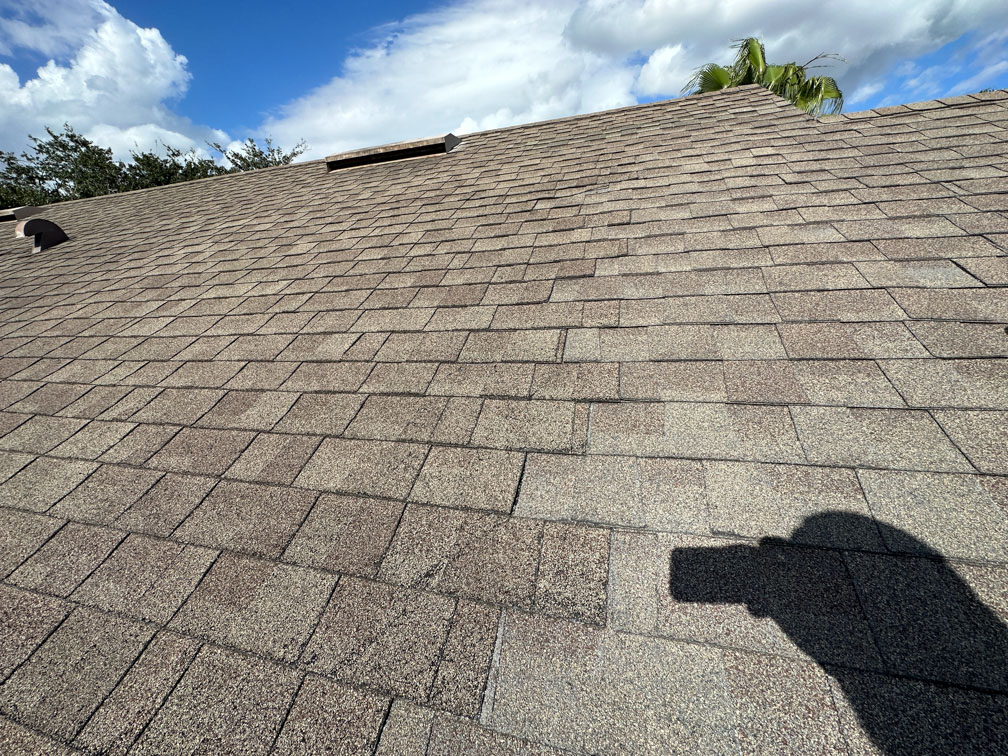 |
This view is looking up the slope of a roof affected by high winds. Some of the shingles were lifted, creased, and torn by the high wind event. |
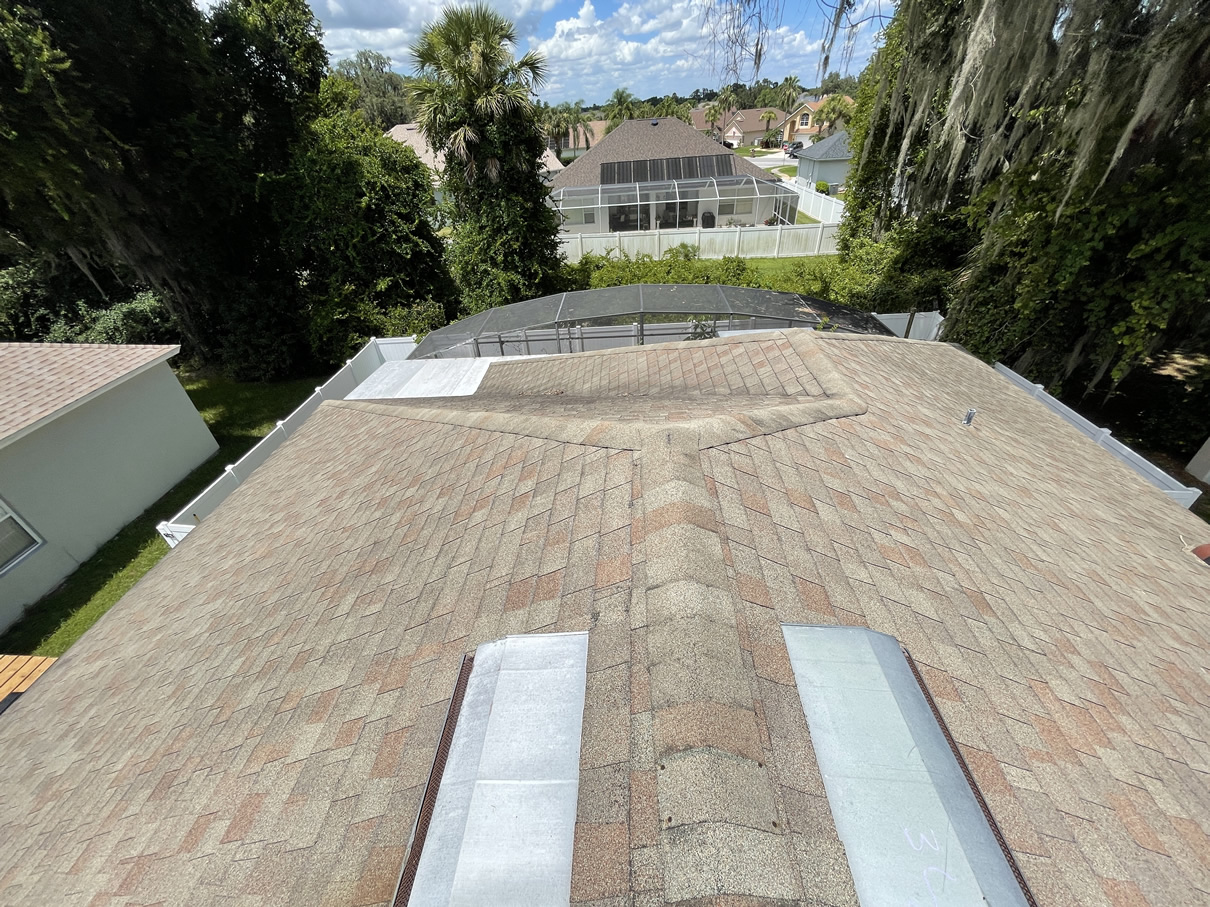 |
The photo depicted is a second roof inspected to confirm the affects of high wind on the roofing material. This roof has surpassed the useful life of a shingle roof in Florida and it should be replaced soon to avoid issues during hurricane season. |
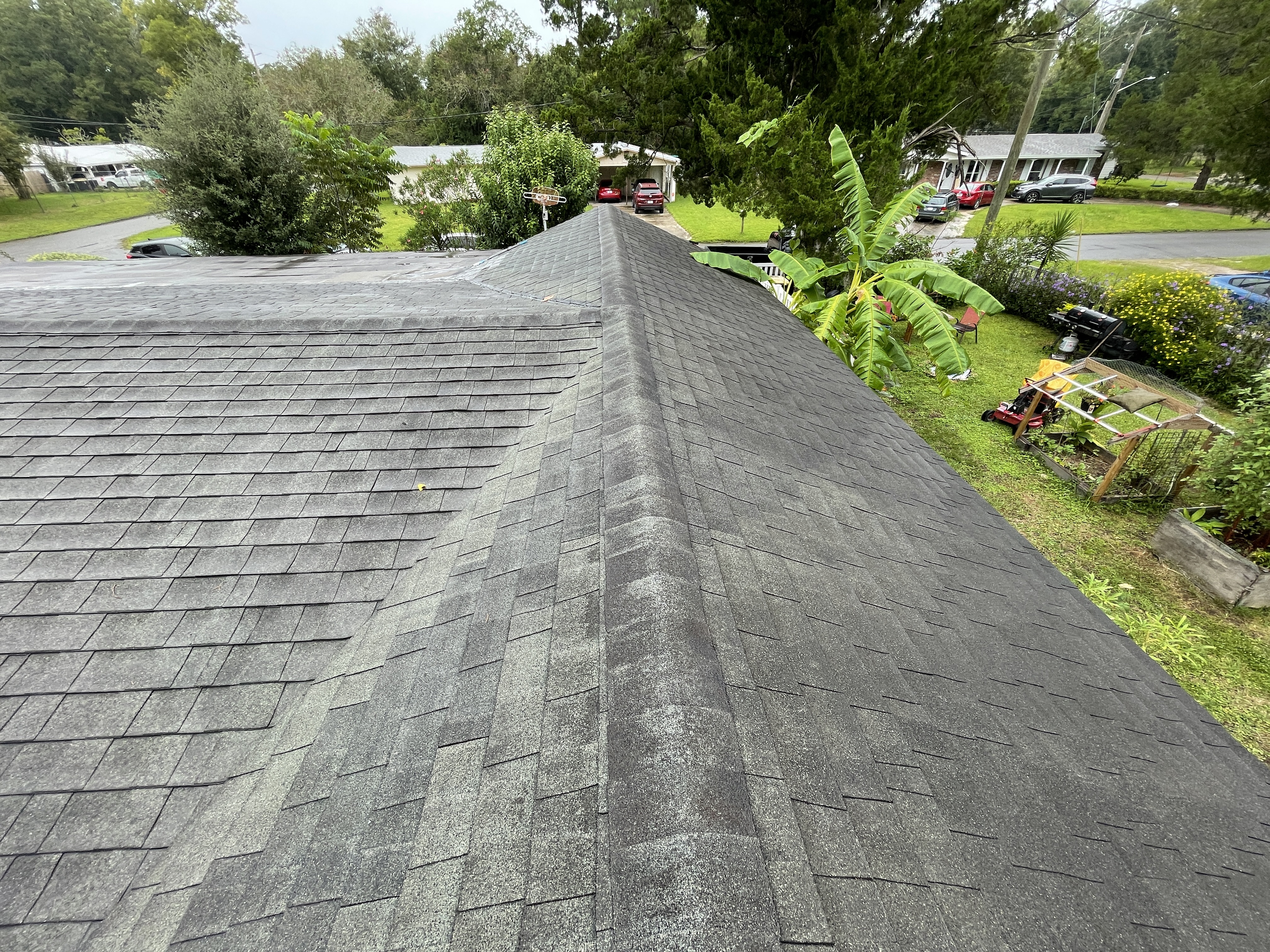 |
Another roof that has surpassed the useful life of a shingle roof in Florida. Like the roof above, this roof should be replaced soon to avoid issues during hurricane season. |
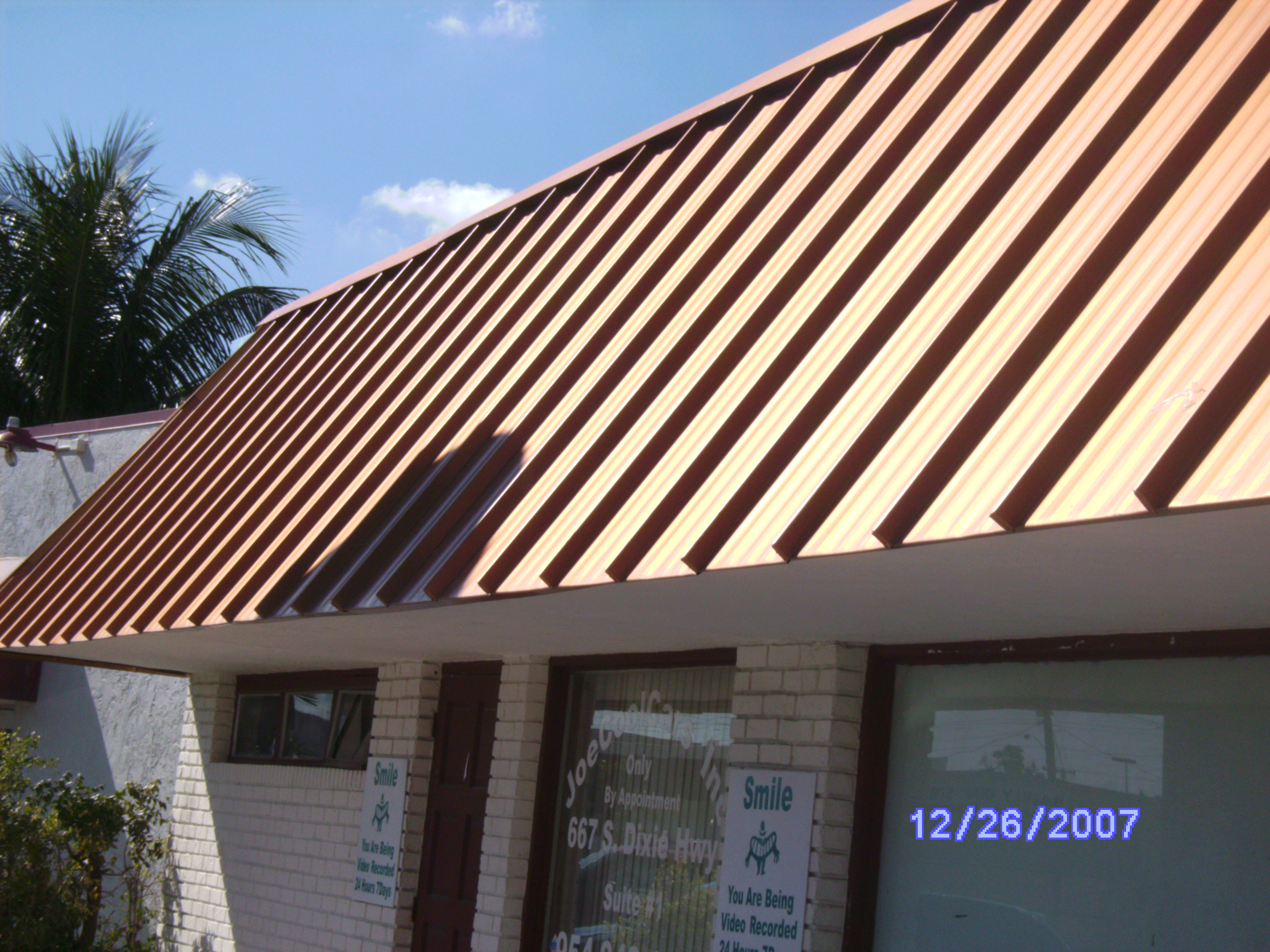 |
This is a copper colored standing seam metal roof. |
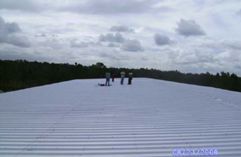 |
This standing seam roof is on a commercial wearhouse. We received 12 semi-truc loads of standing seam material. The project was installed, seamed, and trimmed out in 4 days. |
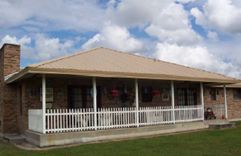 |
Pictured here is a residential metal roof project. The homeowner claims that the AC seems to run less, since installing the styrofoam insulation under the metal roof. |
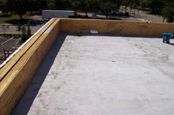 |
The roof pictured here is prepared for a bitumen built up roofing system. This roof was covered with insulation board, bitumen torch down material on the roof and up the walls with a coping cap and cleat along the top of the parapet wall. |
Lake Mary Bridge
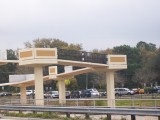 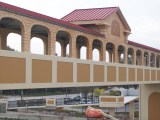
This is a bridge in Orlando. The bridge was for pedestrians and school traffic so schoolchildren did not cross a busy intersection.
We installed the steel support structure for the roof and side panels along with about 550 feet of heavy-duty guardrail shown in the roll over picture to the right.
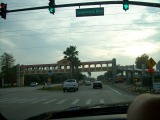
The structure is designed for easy access for handicapped pedestrians. The entire walk area is sloped and staged so the wheel chair bound traveler can make the trek from one side to the other without serious constraints and obstacles hindering the travel.
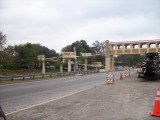
The steel structure on the project was assembled on the road at night and lifted into place. We had to begin work after 6:00 PM and complete the work we did each night before 6:00 AM in order to open the road for traffic the next morning. Some of the nights ran close if something didn't bolt right up.
Remodels are more frequent in recent years.
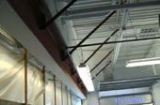 |
Remodels have become more common in recent years. The beam shown here weighs about 7,500 pounds and holds up the roof system for a detail shop at a car dealership. |
|
|
The stair and mezzanine picture is for an addition to a local church. When the project was complete, the total addition was a new drive up and entry to the church. Large glass door and windows, glass handrail, premium tile work, and a full length mezzanine made this section of unusable parking lot into a beautiful entry. |
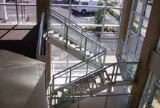 |
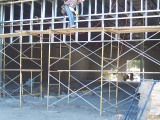 |
As I mentioned on the previous page, these pictures are some of the renovation and modifications that were made to one of the tilt wall buildings. The modifications are part of the rental package for the new tenant, who was extremely pleased once the project was complete.
|
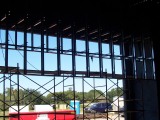 |
Now that you made it to here checking out our site, I would like to thank you for considering us for the construction portion of your project.
21st Century Construction, Inc.
21st Century Construction, Inc. is a small business enterprise with over 40 years experience in the construction industry. We are state licensed and insured.
Our license and insurance information include:
21st Century Construction, Inc.
GENERAL CONTACT INFORMATION
Florida Contact Information
231 Bradshaw Blvd.
Perry FL 32348
9705 Hickory Hollow Rd, Lot 80
Leesburg, FL 34788
- History
- Annealed
- Heat-Treated
- Insulated
- Laminated
- Coated
- Chem Strng
History of Flat Glass Production
In order to better understand the glass and glazing industry, a brief history of glass may be helpful. Glass was discovered over 4000 years ago. It was considered precious and used by royalty and for religious purposes. During the Roman Empire, glass making reached a high degree of quality and use, but declined significantly during the Middle Ages when the main achievement was “stained glass.” In the 7th century, Syrians developed the “crown” method for forming flat glass, whereby the molten glass was taken in lump form and spun on a cylindrical disc to flatten the glass. Interestingly, this represented the most common method to produce flat glass for the next 1000 years. In the early part of the 20th century, inexpensive sheet glass was formed by drawing the glass ribbon vertically out of the molten glass pool. Unfortunately, sheet glass still suffered from distortion because of the differences in viscosity of the molten glass. In order to obtain relatively distortion-free glass for use in coach windows or mirrors, the plate glass process was developed. Plate glass was made by pouring molten glass onto a table and rolling it until flattened, then grinding and polishing it into a plate. This process eventually advanced by feeding the molten glass though continuous rollers, grinders and polishers. Sheet glass is no longer commercially produced in the United States.
In 1959, the float glass process was introduced. This unique glass making process revolutionized the flat glass industry. In the float process, molten glass from the furnace flows by gravity and displacement onto a bath of molten tin where a continuous ribbon is formed. This glass ribbon is pulled or drawn through the tin bath and upon exiting is guided on rollers through an annealing lehr where it is cooled, under controlled conditions, until it emerges at essentially room temperature. The product is now flat, fire-finished and has virtually parallel surfaces. Automatic cutters generally are used to trim the edges and cut across the width of the moving ribbon. This creates sizes, which can be shipped or handled for further processing. The float glass process accounts for almost all of the flat glass presently produced in the United States.
Commercial float glass is nearly colorless with a visible light transmittance ranging from 75% to 92% depending on thickness. With the exception of specialty low-iron glass, a faint green or blue-green color may be noticeable in glazing applications where the glass thickness approaches or exceeds 3/8" (10 mm). Specialty low-iron glass has a higher visible transmittance than commercial float glass of the same thickness. Tinted or Heat-Absorbing Glass is made by adding various colorants to the normal, clear glass batch to create a desired color. The typical colors produced domestically include bronze, gray, dark gray, aquamarine, green, deep green, blue, deep blue and black. Some companies in Europe produce other colors, for instance rose and emerald green. Visible light transmittance will vary from 14% to 85%, depending on color and thickness. The color density is also a function of thickness. As the thickness increases, visible light transmittance will decrease. Tinting reduces the solar transmittance of glass and increases solar heat absorption. Because of this heat buildup, heat-treating (heat-strengthening or tempering) is sometimes required for tinted glass. Color of tinted/heat-absorbing glass is a major consideration for either design and aesthetic reasons or for color matching requirements. Tinted heat-absorbing glass should be viewed as installed for color comparison. Colors may vary considerably among different manufacturers and from run to run. No published color standard exists; the manufacturer should be consulted for color information.
The above information is from the GANA Glazing Manual, 2004 Edition - the most frequently referenced resource in the architectural glass and glazing industry.
Annealed Glass
Upon exiting the tin bath, the float glass ribbon is guided on rollers through an annealing lehr where it is cooled, under controlled conditions, until it emerges at essentially room temperature. The product is now flat, fire-finished and has virtually parallel surfaces. Automatic cutters generally are used to trim the edges and cut across the width of the moving ribbon. This creates sizes that can be shipped or handled for further processing. This glass is referred to as annealed glass.
Annealed glass may be used in its original state or it can be further fabricated by cutting, heat-treating, coating, laminating, or insulating. Annealed glass provides the least resistance to mechanical and thermal stresses when compared with heat-strengthened and fully tempered glass.
Industry production quality requirements, product tolerances and test procedures for annealed glass are defined in the ASTM International (ASTM) document C 1036 Standard Specification for Flat Glass.
The above information is from the GANA Glazing Manual, 2004 Edition - the most frequently referenced resource in the architectural glass and glazing industry.
Production of Heat-Treated Glass
There are two basic methods for producing air-quenched heat-treated glass. The most commonly used heat-treating furnace, a horizontal roller hearth, transports glass on horizontal rollers through the heating and quench processes. A limited amount of heat-treated glass is produced in vertical furnaces, which call for the glass to be held in a vertical position by tongs as it is transported through the heating and quench processes.
Each method produces some degree of bow and warp, which is an inherent characteristic of all heat-treated glass. Tong-held glass, the vertical process, may exhibit a long arc or “S” curve plus some minor distortion at the tong points. Horizontally heat-treated glass will have characteristic waves or corrugations caused by the transport rollers. Industry fabrication requirements, product tolerances and testing procedures for heat-treated glass are defined in the ASTM International (ASTM) document C 1048 Standard Specification for Heat-Treated Flat Glass - Kind HS, Kind FT Coated and Uncoated Glass.
Heat-Strengthened Glass
Heat-strengthened glass is produced with surface and edge compression levels less than fully tempered glass, as specified by ASTM C 1048. The lower compression levels yield a product that is generally twice as strong as annealed glass of the same thickness, size and type. The size and shape of the break pattern of heat-strengthened glass varies with the level of surface and edge compression achieved in the heat-treating process. Heat-strengthened glass with low compression levels will tend to fracture into large fragments, similar to annealed glass breakage. As the compression levels increase, the size of the particles of broken glass tend to become smaller.
ASTM C 1048 requires that heat-strengthened glass have a surface compression level between 3,500 pounds per square inch (psi) to 7,500 psi. The break pattern of heat-strengthened glass is relatively large. The glass pieces typically remain engaged in the glazing pocket, decreasing the probability of fall out. Broken glass should be removed and the opening boarded up or reglazed as soon as possible.
Heat-strengthened glass does not meet the safety glazing requirements of the American National Standards Institute (ANSI) Z97.1 American National Standard for Safety Glazing Materials Used in Buildings - Safety Performance Specifications Method of Test or the federal safety standard Consumer Products Safety Commission 16 CFR 1201 Safety Standard for Architectural Glazing Materials.
Fully Tempered Glass
Fully tempered glass is required in ASTM C 1048 to have either a minimum surface compression of 10,000 psi (69 MPa or an edge compression of not less than 9,700 psi (67 MPa) or meet ANSI Z 97.1 or CPSC 16 CFR 1201. The higher compression levels yield a product that is generally four times stronger than annealed glass and twice as strong as heat-strengthened glass of the same thickness, size and type.
When broken by impact, fully tempered glass immediately disintegrates into relatively small pieces thereby greatly reducing the likelihood of serious cutting or piercing injuries in comparison with ordinary annealed glass. To qualify as a safety glazing material as defined by ANSI Z97.1 and CPSC 16 CFR 1201, the ten largest particles taken from a broken fully tempered lite of glass shall weigh no more than the equivalent weight of 10 square inches (64 sq. cm) of the original specimen when tested according to the standards. Fully tempered glass that meets ASTM C 1048 does not automatically qualify as a safety glazing material.
Note: The GANA Glazing Manual should be consulted for additional information on Safety Glazing in Hazardous Locations (Section V, page 33) and Design Considerations (Section II - Fabricated Architectural Glass Products, page 9) when specifying and using heat-treated glass.
The above information is from the GANA Glazing Manual, 2004 Edition - the most frequently referenced resource in the architectural glass and glazing industry.
Insulating Glass
In order to reduce heat gain or loss through glass, two or more lites may be sealed together to create an insulating glass (IG) unit.
The majority of insulating glass units consist of two lites of glass enclosing a hermetically sealed air space. The lites are held apart by a spacer around the entire perimeter. The spacer contains a moisture-adsorbent material called desiccant that serves to keep the enclosed air free of visible moisture. The entire perimeter of the assembly is sealed.
The most commonly used edge construction contains a metallic spacer of roll-formed aluminum, stainless steel, coated steel or galvanized steel. It is sealed with a single seal of polysulfide, polyurethane or hot-melt butyl, or with a dual seal consisting of a primary seal of polyisobutylene and a secondary seal of silicone, polysulfide or polyurethane. The corners of the metallic spacer may be square-cut and joined with a metal, plastic or nylon corner key, may be miter-cut and brazed, welded or soldered, or may be bent. Recent years have seen the introduction of warm edge technology products as spacer materials. These products include extruded butyl materials, foam rubber based materials, formed plastics and metal strip based products, many with desiccant included as a component.
Improvements in edge of insulating glass U-values as a result of warm-edge technologies play a vital role in meeting overall window performance requirements for state adopted residential fenestration codes.
Thermal performance of insulating glass units is enhanced by using solar control substrates and coated glass (low-emissivity or reflective), coated polyester suspended films, insulating gases (such as argon, krypton or xenon) and warm edge technology products. Initial heating and cooling equipment costs and ongoing operating costs are reduced.
Insulating glass units also offer benefits by reducing sound transmission. Laminated glass constructions and sulfur hexafluoride (SF6) gas filling further enhance the sound reduction characteristics of the insulating glass unit.
Industry product classification, performance requirements and testing procedures for insulating glass units are defined in the following ASTM International documents:
E 773 Standard Test Method Accelerated Weathering of Sealed Insulating Glass Units
E 774 Standard Specification for Sealed Insulating Glass Units
E 2188 Standard Test Method for Insulating Glass Unit Performance
E 2189 Standard Test Method for Testing Resistance to Fogging in Insulating Glass Units
E 2190 Standard Specification for Insulating Glass Unit Performance and Evaluation
Most insulating glass fabricators voluntarily participate in insulating glass certification programs. The purpose of the certification programs is to assure the user that the purchased product is a faithful replica of one that has passed certain prescribed tests. Therefore, participants in a certification program must complete the following requirements: 1) submit specimens of their production product to independent testing laboratories for the prescribed tests; and 2) agree to periodic, unannounced inspections of their regular production by an independent agency to ensure that actual production employs the same materials and techniques as the tested specimen.
The Insulating Division of the Glass Association of North America (GANA) and the Insulating Glass Manufacturers Alliance (IGMA) promote the highest standards in insulating glass unit production, testing, certification and business ethics through their memberships. The industry establishes voluntary quality standards and collects statistical and other non-proprietary information related to field performance of insulating glass for dissemination to manufacturers and consumers.
Note: The GANA Glazing Manual (Section II - Fabricated Architectural Glass Products) should be consulted for additional detailed information on insulating glass design considerations, material compatibility and glazing guidelines prior to specifying and using insulating glass constructions.
The above information is from the GANA Glazing Manual, 2004 Edition - the most frequently referenced resource in the architectural glass and glazing industry.
Laminated Glass
Laminated glass is traditionally defined as:
1.Two or more lites of glass and one or more interlayers of plasticized polyvinyl butyral (PVB) permanently bonded together under heat and pressure;
2.Two or more lites of glass and polycarbonate with an aliphatic urethane interlayer between glass and polycarbonate permanently bonded together under heat and pressure.
3.Two or more lites of glass bonded with one or more interlayers of a liquid resin cured and permanently bonded together by exposure to ultraviolet light, heat, or chemicals.
4.Two or more lites of glass with an ionoplast rigid sheet interlayer (similar to a PVB yet more rigid) permanently bonded together under heat and pressure.
5.Two or more lites (or sheets) of polycarbonate (or acrylic) with an aliphatic urethane interlayer between polycarbonate or acrylic bonded together under heat and pressure.
6.Two or more lites and polyester (PET) film with a polyvinyl butyral (PVB) interlayer between glass and PET permanently bonded together under heat and pressure.
Annealed, heat-treated, chemically strengthened, wired, tinted, patterned and coated glass, as well as one- and two-way mirrors, can be incorporated into the laminated unit.
This union of materials provides a variety of performance benefits in architectural, security and other specialty applications. Its most important characteristic is the ability of the interlayer to support and hold the glass when broken and/or plastic sheet when cracked. This provides for increased protection against fall-out and penetration of the opening. Most building codes require the use of laminated glass for overhead glazing as monolithic lites, or as the lower lite in multiple glazed units. Other applications include safety, security, detention, seismic-resistant, blast-resistant, bullet-resistant, burglary-resistant, hurricane/cyclic wind-resistant and sound reduction applications. Laminated glazing materials are also used in specialty applications such as aquariums, animal enclosures, glass stairs, floors and sports stadiums.
Laminated glass with PVB interlayers are generally 75% to 100% as strong as annealed glass of the same thickness depending on exposed temperatures, aspect ratio, plate size, stiffness and load duration. Laminated glass, however, can be made with heat-strengthened, fully tempered or chemically strengthened glass for additional benefits, such as increased wind-load resistance, impact resistance, or resistance to thermal stress. The ability of the interlayer to resist various kinds of penetration may also be dependent upon thickness, temperature and other variables. Check with the fabricator for any additional limitations, such as roll distortion, that may result from this additional processing of laminated glass. There are several grades of PVB having different physical properties. Care should be taken to specify the correct grade for a given application. Consult the interlayer manufacturer / glass fabricator for full details. Typical applications for laminated glass with PVB interlayers and cured resins include locations where safety glazing is required, such as doors and skylights, shower and bath doors and enclosures. Other locations where safety glazing may be specified include operable windows and fixed glazed panels, balconies, railing systems, elevators, sports stadiums, atriums, greenhouses, skylights and sloped glazing. Laminated glass resists glass fall-out from windblown debris in hurricane / cyclic-windstorm prone areas and provides various levels of security protection in seismic, blast-resistant, bullet-resistant and burglary-resistant applications.
Laminated glass with ionoplast interlayers are similar to PVB laminates; however, the rigid interlayer provides additional performance in high design pressure and high security applications where lower deflections and higher penetration resistance is required after the glass lites have been broken.
Glass-clad polycarbonate contains glass layers to the exterior and one or more polycarbonate layers on the inside. This product combines the heat, chemical and abrasion resistance of glass with the impact resistance of polycarbonate. This laminated construction may also be unbalanced or asymmetrical, where a polycarbonate layer is exposed to the interior. Although not truly a “glass-clad” product, the industry recognizes the product under the same category. Glass-clad polycarbonates provide resistance to forced entry and ballistics and are commonly used in prisons, detention centers, jails, psychiatric facilities and other architectural settings where security is a primary concern.
Organic coated glass-butyral consist of at least one lite of glass with its interior or protected surface laminated under heat and pressure to a composite sheet of PVB with a scratch-resistant polyester (PET) film. Optionally, the organic coated glass-butyral can be applied onto multiple-ply laminated glass. The composite organic coating consists of an abrasion resistant polyester-film combined with a sheet of PVB for factory lamination to glass. The PVB is used to adhere the PET film to the glass surface. The composite must face towards the building’s interior. These laminates are generally used in security applications where there is a requirement for zero spalling on the inside of a building or room following attack from the outside.
Polyester (PET) films can also be laminated inside the laminated glass using polyvinyl butyral (PVB) to bond the PET to the glass. This PET film can provide additional resistance to penetration and cyclic wind pressure.
Quality standards for laminated glass are defined in ASTM C 1172 Standard Specification for Laminated Architectural Glass and ASTM C 1349 Standard Specification for Architectural Flat Glass Clad Polycarbonate. Laminated glass for use as safety glazing is covered by ANSI Z97.1 and CPSC 16 CFR 1201 Cat. I and II.
Note: The GANA Glazing Manual and Laminated Glazing Reference Manual should be consulted for additional detailed information on laminated glass, burglar-resistant, bullet-resistant, and physical-attack resistant laminated constructions prior to specifying and using laminated glass constructions.
The above information is from the GANA Glazing Manual, 2004 Edition - the most frequently referenced resource in the architectural glass and glazing industry.
Coated Glass
Flat glass products may be coated to enhance the thermal and optical performance characteristics of products used in residential and commercial glazing, and transportation applications. There are two basic types of coated glass: solar control (reflective) and low-emissivity (low-e). The major differences are visible light transmission, UV, visible, and near infrared wavelengths of energy that are reflected and the directions in which these wavelengths are usually reflected.
The solar spectrum consists of ultraviolet light with wavelengths ranging from 300-390 nm, visible light (390-770 nm) and infrared light (770-2100 nm). The distribution of energy within the solar spectrum is approximately 2% ultraviolet (UV), 46% visible and 52% infrared (IR).
Solar-control glass may have a variety of metal coating layers that are highly reflective of solar energy, i.e., those energy wavelengths from 300-2100 nanometers (nm) that constitute the solar spectrum.
The major benefits of reflective solar control glass include the following:
Aesthetic appeal: Colors of silver, blue, copper, golden and earth-tone coatings, applied to the wide range of clear and tinted float glass, allows the architect considerable flexibility with exterior design.
Energy savings: through its ability to reflect, absorb and radiate solar energy, solar reflective glass substantially reduces interior solar heat gain. The added cost of the coating will generally be offset by the reduced size and operating cost of the heating and cooling systems.
Occupant comfort: is improved when heat gain is reduced and interior temperatures are easier to control.
Low-emissivity (low-e) coated glass may have various combinations of metal, metal oxide and metal nitride layers of coatings that are nearly invisible to the eye. Some low-e coatings are highly reflective for the infrared (IR) part of the solar spectrum and all low-e coatings reflect long wave IR energy. Long wave IR can be described as the radiant heat given off by an electric coil-type heater, as well as the heat that comes from a hot air register. The re-radiated heat from room furnishings that have absorbed solar energy is still another form of radiant heat.
While some low-e coatings can be used in monolithic or laminated glass constructions, the coatings provide maximum performance when sealed within an insulating glass unit. The location of the low-e coating within a unit affects the product performance. A low-e coating on the second (#2) surface of an insulating glass unit is more effective at reducing solar heat gain, especially when used in conjunction with tinted glass. The low-e coating will reflect re-radiated heat (IR), while the tinted glass reduces the solar radiation through the glass, resulting in less glare and heat gain. When using low-e glass in commercial buildings and residential applications in warm climate regions, this is generally the most practical way to maintain comfort levels.
In cold climate regions where building owners and occupants want to maximize solar heat gain from the sun while minimizing radiant heat loss, insulating glass units commonly incorporate clear glass with a low-e on the third (#3) surface. The low-e coating reduces heat loss through the glass in winter by reflecting interior long wave IR back into the home or office.
Center of glass U-values in the range of 0.25 - 0.36 can be achieved with low-e coatings on the second or third surface of insulating glass units. Low-e coatings can be combined in an insulating unit with a solar-control / reflective coating and gas filling to create an insulating unit having lower U-values and a lower shading coefficient. Since technology continues to advance and because the combinations of substrates and coatings are too numerous to list, it is best to consult the coated glass manufacturers’ published literature for comparisons. A generic listing of U-values of various glazing products is provided in the GANA Glazing Manual.
The major benefits of low-e coated glass are:
Aesthetic Appeal: the virtually invisible nature of low-e coatings provide a transparent appearance to the glazing material and building façade.
Energy Savings: through its ability to reflect long-wave infrared energy low-e coated glass reduces winter heat loss and summer heat gain through the glass, and provides high levels of visible light transmittance into the building. The combination of thermal control and reduction in interior lighting requirements reduces energy consumption for residential, and commercial buildings.
Occupant Comfort: is improved when heat gain/loss is reduced by keeping the interior temperature stable regardless of the exterior environment and when natural daylight is introduced into the building.
Optical and aesthetic quality requirements for coatings applied to glass are addressed in ASTM C 1376 Standard Specification for Pyrolytic and Vacuum Deposition Coatings on Flat Glass.
Note: The GANA Glazing Manual should be consulted for additional detailed information on Coating Methods, Specifications and Coating Imperfections (Section II - Fabricated Architectural Glass Products, pages 14 & 15) prior to specifying and using coated glass.
The above information is from the GANA Glazing Manual, 2004 Edition - the most frequently referenced resource in the architectural glass and glazing industry.
Chemically Strengthened Glass
Chemical strengthening of glass is produced through a process known as ion-exchange. One of the methods used to chemically strengthen glass calls for the lites to be submersed in a molten salt bath at temperatures below the strain point of the glass. In the case of soda-lime float or soda-lime sheet glass, the salt bath consists of potassium nitrate. During the submersion cycle, the larger alkali potassium ions exchange places with the smaller alkali sodium ions in the surface of the glass. The larger alkali potassium ions “wedge” their way into the voids in the surface created by the vacating smaller sodium ions.
Chemically strengthened glass production requirements and test procedures are defined in ASTM C 1422 Standard Specification for Chemically Strengthened Flat Glass. The specification covers the requirements for chemically strengthened glass products, which originate from flat glass for use in building construction, transportation and other specialty applications.
Under the specification, chemically strengthened glass is classified on the basis of independent levels of surface compression and case depth. Increasing levels of surface compression permit an increasing amount of flexure. Greater case depths provide increased protection from strength reduction caused by abuse and abrasion. Consumers should consult with chemically strengthened glass fabricators regarding the recommended surface compression and case depth levels required for their individual application. Product classification levels may be confirmed through laboratory testing in accordance with the specification.
Chemically strengthened glass can be significantly stronger than annealed glass, depending upon the glass product, strengthening process, level of abrasion, and the application. Chemically strengthening glass is often the alternative to thermal tempering when applications call for glass that is very thin, small in size, or complex in shape.
Although chemically strengthened glass can be cut after treatment, it is not recommended, as edge strength will be reduced to that of annealed glass.
When broken by impact, chemically strengthened glass exhibits a break pattern similar to annealed glass, and therefore, does not meet safety-glazing requirements in a monolithic form. When safety-glazing performance is required, chemically strengthened glass should be laminated.
While chemically strengthened glass is often used monolithically, product usage has increased in laminated constructions for security, detention, hurricane/cyclic wind-resistant, blast and ballistic-resistant glazing applications.
The above information is from the GANA Glazing Manual, 2004 Edition - the most frequently referenced resource in the architectural glass and glazing industry.
- Timothy G Cooprider
- Education
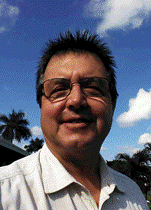
HI
I’M TIM
President of
21st Century Construction, Inc.
A resident of Florida since 1974, a State Certified General Contractor CGC1527754, State Certified Building Contractor CBC1251651 and State Certified Roofing Contractor CCC1326365, Licensed Insurance Adjuster P158468, State Licensed CAM CAM51607, a Federally Approved 203K Consultant, and a Federally Approved HUD Inspector; now with that bit of information you have a little background on your contractor.
The founder of 21st Century Construction, Inc. and KTG Property Solutions, Inc.
Well versed in MS Office, AutoCAD, and the ADOBE suite for the office and the web.
21st Century Construction, Inc. offers estimates at no charge and a detailed report for all work.
Timothy G Cooprider
1994-1997 USF Lakeland and Winter Haven, FL Computer Science
Classes to secure a Bachelors Degree in Computer Science.
2002-2003 Contractors Institute, Inc. Orlando, FL Construction and building trade
Specific classes for the Certified Building Contractor License, the 3 week course prepared the student for the General Contractor’s state exam; the only grade received was a pass or fail on the state test.
2004-2005 Contractors Institute, Inc. Orlando, FL Construction and roofing trade
Specific classes for the Certified Roofing License, the 1 week course prepared the student for the Roofing Contractor’s state exam; the only grade received was a pass or fail on the state test.
2008 University of Florida Orlando, FL Wind and Hurricane Mitigation (Certificate of Completion)
Certified inspector for wind mitigation under the guidelines of My Safe Florida Home and the State of Florida. This certifies me to do inspections and fill out the forms for homeowners and insurance companies to insure the structure meets the minimum requirements for the current wind fortification standards.
2007-2008 University of Central Florida On line Accredited Claims Adjuster course
This 40 hour course returned a Florida Adjusters License; a 520 all lines license and ample experience in Activate, an estimating program used by the insurance industry.
2009 Certified Renovators Course This 8-hour course returned an EPA Certified Renovator status for the Repair Remodel Paint class.
2017 Attended classes to complete the flood certification course. Received a Flood Certification Number 0070007138
Attended classes to complete the HAAG Certified Wind Inspector course. Very educational and explained the affects of wind on structures. The course offered a certification number, 992006043 HAAG Certified Wind Inspector
TRIA Certified High Wind Manual 6th Edition is a certification for tile roof installation to ensure the proper methods are being applied to better battle the high winds experienced here in Florida.
Attended classes to complete the UAS Remote Pilot for opperating a drone commercially. The course offered enough class time to take the FAA test and secure a certification number, 4336479 UAS Remote Pilot
|